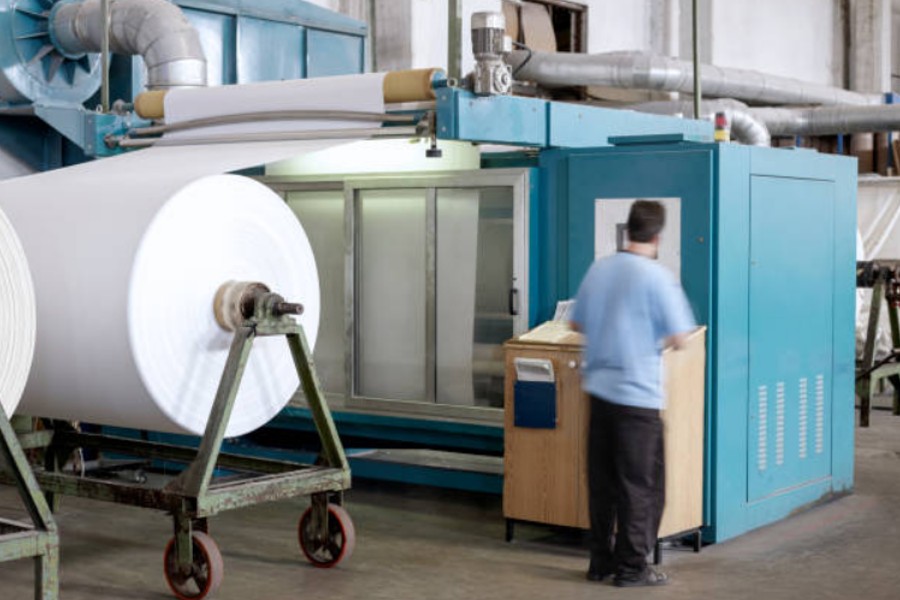
Ball mills are used in the grinding of materials and can be of two types, wet and dry.
Each of the methods has its advantages and limitations depending on the situation and the nature of the business, especially in the case of a rock crusher factory where the handling of materials is crucial. This paper aims at comparing the pros and cons of wet and dry ball mills based on real-life practices of the industry, including those of batch ball mill manufacturers.
Energy and Work Indexes
Wet ball mills are comparatively more energy intensive due to the resistance offered by the liquid slurry and hence the operating expenses are high. But it is worth to note that the addition of water during grinding can help in the grinding process and hence reduce the total energy needed. Dry ball mills, although less energy demanding, may result in higher energy consumption in the long run because of wear and tear without the help of fluids.
Transportation
Wet ball mills are used when the material to be ground is very hard and/or very fibrous because the water in the mill acts as a lubricant and prevents the material from sticking to the balls. This method also reduces the amount of dust produced hence making it an environmentally friendly method. Dry ball mills are less sensitive to the feed size and produce a finer product but they are prone to overheating and the material being processed may be altered or damaged.
Maintenance and Operational Costs
Wet ball mills are more demanding in terms of maintenance since the wet environment is corrosive and thus accelerates the wear of the mill components. They also entail sophisticated handling of waste water. Dry ball mills are easier to maintain since they do not use fluids; however, dust and heat must be closely monitored to avoid system breakdowns.
Environmental and Regulatory Compliance
Another factor that may affect the decision between wet and dry milling is environmental concerns. Wet milling is less likely to cause air pollution compared to dry milling, although the latter can be problematic in terms of dust emissions; however, wet milling is more likely to cause water pollution and is less preferred in areas where water is scarce.
- Lincoln Theodore Monroe Andrew Perry, “Stepin Fetchit,” The Rise And Fall Of The First Black Super Star, 1902 – 1985
- Sponsored Love: AARP Plan F Benefits, What You Need To Know?
- Discover 5 Reasons Of Class Events Is Perfect For Your Special Day
- Jean Shafiroff Honored At 25th Celebration Of The James Jay Dudley Luce Foundation
- Boston: Smino Honored With Lifetime Achievement Award By Harvard’s Black Men’s Forum
Collaboration
Working with a rock crusher factory and a batch ball mill factory can help to find ways to create new milling solutions that meet the needs of an operation. Such collaborations can assist in enhancing the wet and dry milling operations to obtain the most favorable results in terms of productivity, cost, and sustainability.
When choosing between wet and dry ball mills, the manufacturers have to take into account the requirements of the process, the conditions under which the process will be conducted, and the impact on the environment. When these factors are properly assessed, it is possible to select the most appropriate milling option that will be suitable for the business’ strategic plans and operations.
Become a Harlem Insider!
By submitting this form, you are consenting to receive marketing emails from: . You can revoke your consent to receive emails at any time by using the SafeUnsubscribe® link, found at the bottom of every email. Emails are serviced by Constant Contact