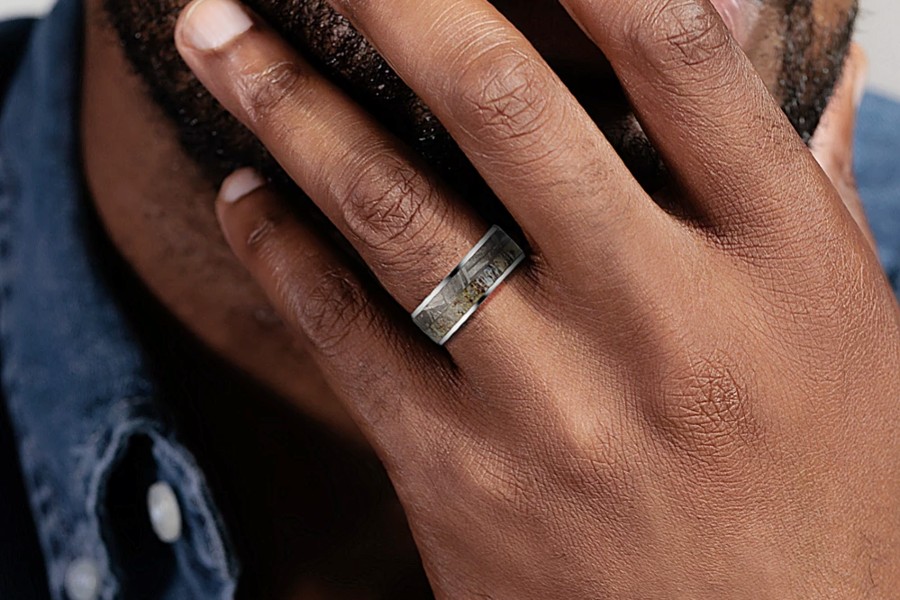
When it comes to selecting the perfect metal for your project, the choice often boils down to two titans of the material world: Tungsten and Titanium.
Both metals boast impressive qualities, making them favorites across various industries. But how do you decide which one is right for your specific needs? Let’s dive deep into the world of Tungsten and Titanium, exploring their unique characteristics, advantages, disadvantages, and applications to help you make an informed decision.
What Is Tungsten?
Tungsten, known for its remarkable resilience, stands out in the metal kingdom. Its physical and chemical properties make it a powerhouse in numerous applications.
Physical and Chemical Properties
- Highest Melting Point: Tungsten boasts the highest melting point of all metals at a staggering 3422°C. This extraordinary feature allows it to maintain its integrity under extreme heat, making it indispensable in high-temperature environments.
- Exceptional Hardness: Tungsten is incredibly hard, almost rivaling the hardness of diamond. This makes it an excellent choice for applications that require materials resistant to wear and tear.
- Excellent Conductivity: With superb electrical and magnetic conductivity, Tungsten efficiently conducts electricity, making it valuable in various electronic applications.
- Corrosion Resistance: Tungsten’s resistance to corrosion ensures its longevity, even in harsh environments, reducing the need for frequent replacements.
Advantages
- High Melting Point and Tensile Strength: Tungsten’s ability to withstand high temperatures and immense stress makes it ideal for applications that demand durability and strength.
- Superior Hardness and Wear Resistance: Its hardness ensures that Tungsten-based tools and components last longer, maintaining their performance over time.
- Excellent Electrical and Thermal Conductivity: These properties make Tungsten a preferred material in electrical and electronic industries, where efficient energy transfer is crucial.
Disadvantages
- High Density: Tungsten is notably heavy, with a density of 19.27 g/cm³. This high weight can limit its use in applications where weight is a critical factor.
- Cost: Compared to other industrial metals, Tungsten is more expensive, which can be a significant consideration for budget-conscious projects.
- Processing Challenges: Tungsten’s high melting point makes it difficult to process and form, requiring specialized equipment and techniques.
Common Applications
Tungsten’s unique properties make it a versatile material across various industries:
- Jewelry Manufacturing: Particularly in everyday wear like rings, Tungsten’s hardness ensures jewelry remains scratch-free and durable.
- Aerospace: Used in high-temperature and high-stress components like rocket engines and military equipment.
- Medical Devices: Employed in X-ray shields, anti-scatter plates, and radiation source containers due to its density and hardness.
- Electronics: Ideal for filaments, semiconductor devices, and components that require high density and low toxicity.
- Industrial Tools: Utilized in cutting tools, mining tools, and abrasives because of its exceptional wear resistance.
What Is Titanium?
Titanium is celebrated for its blend of strength and lightweight properties. It’s a metal that combines durability with versatility, making it a favorite in many high-performance applications.
Physical and Chemical Properties
- High Strength-to-Weight Ratio: Titanium offers impressive strength while being significantly lighter than many other metals. This makes it ideal for applications where weight savings are essential without compromising strength.
- Corrosion Resistance: Titanium excels in resisting corrosion, particularly in environments exposed to harsh chemicals and salty conditions.
- High-Temperature Resistance: It maintains its properties and performance even at elevated temperatures, making it suitable for high-heat applications.
- Acid Resistance: Titanium shows excellent resistance to dilute acetic and hydrochloric acids, enhancing its durability in corrosive environments.
Advantages
- Lightweight Yet Strong: The combination of low density and high strength makes Titanium perfect for applications where reducing weight is crucial, such as in aerospace and automotive industries.
- Superior Corrosion Resistance: Titanium’s ability to resist corrosion extends the lifespan of products, especially those exposed to moisture and chemicals.
- High-Temperature Performance: It performs reliably in high-temperature settings, maintaining structural integrity where other metals might fail.
Disadvantages
- Cost: Titanium is relatively expensive compared to other metals, which can be a limiting factor for some applications.
- Processing and Welding Challenges: Working with Titanium requires specialized techniques and equipment, making fabrication more complex and costly.
Common Applications
Titanium’s remarkable properties open doors to a wide range of applications:
- Aerospace Industry: Used in aircraft parts, engines, and structural components where strength and weight are critical.
- Automotive Industry: Employed in high-performance vehicles for components that benefit from reduced weight and increased strength.
- Medical Technology: Ideal for biocompatible implants and surgical tools due to its non-reactive nature and strength.
- Industrial Applications: Utilized in environments that demand high corrosion resistance and durability, such as chemical processing plants.
Key Differences Between Tungsten and Titanium
While both Tungsten and Titanium are exceptional metals, they cater to different needs based on their distinct properties. Understanding these differences is key to selecting the right material for your application.
Melting Point
- Tungsten: 3422°C
- Titanium: 1688°C
Tungsten’s significantly higher melting point makes it suitable for applications involving extreme heat, whereas Titanium’s lower melting point allows for easier processing but limits its use in ultra-high-temperature environments.
Density
- Tungsten: 19.27 g/cm³
- Titanium: 4.506 g/cm³
Tungsten is nearly four times denser than Titanium. This high density provides excellent mass and stability but makes Tungsten unsuitable for weight-sensitive applications where Titanium shines.
Tensile Strength
- Tungsten: 980 MPa
- Titanium: 240 MPa
Tungsten’s superior tensile strength means it can withstand higher stresses without deformation, making it ideal for high-stress applications. Titanium, while strong, offers a better strength-to-weight ratio, balancing strength with reduced weight.
Corrosion Resistance
- Tungsten: Good
- Titanium: Excellent
While both metals resist corrosion, Titanium outperforms Tungsten, especially in acidic environments. This makes Titanium the preferred choice in applications exposed to corrosive substances.
Weight
- Tungsten: Heavy
- Titanium: Lightweight
Titanium’s lightweight nature makes it ideal for applications where reducing weight is essential, such as in aerospace and automotive industries. Tungsten’s heaviness, however, provides stability and mass, beneficial in applications like counterweights and ballast.
Processing Ease
- Tungsten: Difficult due to high melting point
- Titanium: Easier due to lower melting point
Titanium is easier to process and form, thanks to its lower melting point. Tungsten requires specialized equipment and techniques, making its fabrication more challenging and costly.
Applications of Tungsten
Tungsten’s unique properties make it indispensable across a variety of industries. Let’s explore some of its most common applications.
Metal Casting
In metal casting, Tungsten is added to steel and superalloys to significantly enhance their hardness, wear resistance, and corrosion resistance. This application alone accounts for over 20% of global Tungsten consumption, highlighting its importance in producing durable and high-performance metals.
Abrasives and Cutting Tools
Tungsten carbide, a compound of Tungsten and Carbon, is renowned for its extreme hardness and wear resistance. It’s a staple in manufacturing cutting tools, mining tools, and abrasives. Whether you’re slicing through metal or mining rock, Tungsten carbide tools deliver the precision and durability required for tough jobs.
Electronics
The electronics industry leverages Tungsten for its excellent electrical and thermal conductivity. It’s used in filaments, semiconductor devices, and other components where efficient energy transfer and durability are paramount. Tungsten’s high density and low toxicity further enhance its suitability for electronic applications.
Aerospace
In the aerospace sector, Tungsten is essential for manufacturing components that operate under high temperatures and pressures, such as rocket engines and military equipment. Its ability to maintain structural integrity in extreme conditions ensures the reliability and performance of aerospace machinery.
Medical Devices
Tungsten’s high density and hardness make it ideal for medical applications, including X-ray shields, anti-scatter plates, and radiation source containers. These devices benefit from Tungsten’s ability to block harmful radiation and maintain durability over extended use.
Industrial Tools
From cutting tools to mining equipment, Tungsten-based alloys are integral to producing durable industrial tools. Its wear resistance ensures that tools last longer and perform consistently, even in the most demanding environments.
Wear-Resistant Alloys
Tungsten is often mixed with other metals like Chromium, Cobalt, and Carbon to create wear-resistant alloys. These alloys are used in producing turbine blades, engine valves, and other components that endure constant friction and stress, ensuring longevity and performance.
Applications of Titanium
Titanium’s blend of strength, lightness, and corrosion resistance makes it a versatile material across multiple industries. Here’s a closer look at where Titanium shines.
Aerospace
In the aerospace industry, Titanium is prized for its lightweight yet strong properties. It’s used in manufacturing aircraft parts, engines, and structural components where reducing weight without compromising strength is crucial. Titanium’s ability to withstand extreme conditions ensures the safety and efficiency of aircraft.
Automotive
High-performance vehicles benefit from Titanium’s strength-to-weight ratio. It’s used in engine components, exhaust systems, and other parts where reducing weight can enhance speed and fuel efficiency. Titanium’s durability also ensures that automotive parts last longer under constant stress and heat.
Medical Technology
Titanium’s biocompatibility makes it ideal for medical implants and surgical tools. From joint replacements to dental implants, Titanium’s ability to integrate with human tissue without causing adverse reactions ensures patient safety and comfort. Its strength and lightness also make surgical tools more manageable and effective.
Industrial Applications
In industrial settings, Titanium is used in environments that demand high corrosion resistance and durability. It’s found in chemical processing plants, desalination units, and other facilities where exposure to corrosive substances is common. Titanium’s resilience ensures that components maintain their integrity and functionality over time.
Marine Applications
Titanium’s resistance to seawater corrosion makes it suitable for marine applications, including shipbuilding, offshore oil rigs, and underwater equipment. Its ability to withstand harsh marine environments ensures the longevity and reliability of marine structures and devices.
Sports Equipment
Titanium is increasingly used in sports equipment, such as golf clubs, bicycles, and tennis rackets. Its lightweight and strong properties enhance performance while ensuring durability, providing athletes with equipment that can withstand rigorous use.
Choosing Between Tungsten and Titanium
Deciding between Tungsten and Titanium hinges on the specific requirements of your application. Here’s a guide to help you choose the right metal based on your needs.
When to Choose Tungsten
- Extreme Temperature Requirements: If your application involves exposure to very high temperatures, Tungsten is the go-to choice due to its unparalleled melting point.
- High Tensile Strength Needs: For applications that require materials to withstand significant stress without deforming, Tungsten’s high tensile strength makes it ideal.
- Wear and Abrasion Resistance: When durability and resistance to wear are paramount, Tungsten-based tools and components ensure longevity and consistent performance.
- Mass and Stability: In applications where adding weight for stability is beneficial, such as in counterweights or ballast, Tungsten’s high density provides the necessary mass.
When to Choose Titanium
- Lightweight Requirements: If reducing weight without sacrificing strength is crucial, Titanium’s high strength-to-weight ratio makes it the superior choice.
- Corrosion Resistance Needs: For environments exposed to moisture, chemicals, or salty conditions, Titanium’s excellent corrosion resistance ensures durability and longevity.
- Biocompatibility: In medical applications where the material needs to integrate with human tissue, Titanium’s biocompatibility is essential.
- Ease of Processing: If your project requires easier fabrication and forming, Titanium’s lower melting point compared to Tungsten simplifies processing and reduces manufacturing costs.
Latest Posts
- Los Angeles: Yuletide Cinemaland, A Festive Celebration Of Holiday Spirit
- Sponsored Love: Deck The Halls With Savings, Instacart’s Holiday Cheer Is Here!
- Mayor Adams And Governor Hochul Remove 73,000 Ghost Cars From NYC
- Federal Trade Commission (FTC) Warns Companies Not To Misrepresent Health Plans
- Governor Hochul Enacts Law Mandating Insurance Coverage For Dyslexia Testing
Become a Harlem Insider!
By submitting this form, you are consenting to receive marketing emails from: . You can revoke your consent to receive emails at any time by using the SafeUnsubscribe® link, found at the bottom of every email. Emails are serviced by Constant Contact